MILITARY ∙ MEDICAL ∙ AEROSPACE ∙ ELECTRONICS ∙ SEMICONDUCTOR ∙ CONSTRUCTION
ABOUT OUR CHEM FILM SERVICES IN PHOENIX, AZ
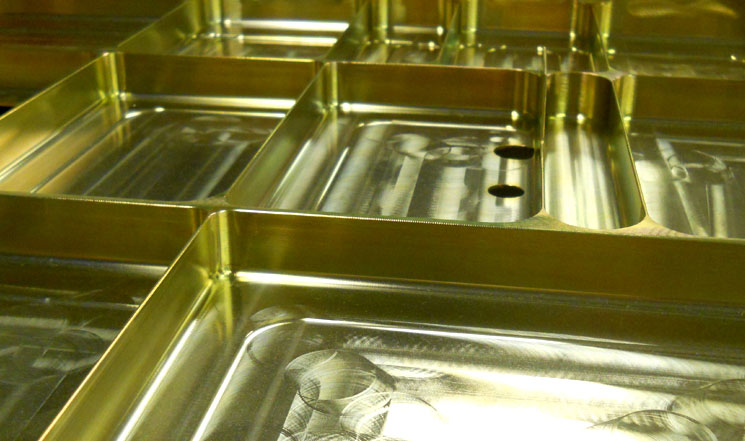
Chem film is a class of durable and inexpensive sealant coatings which adhere to metal surfaces to protect them from corrosion. Even though we often think that the last coat that is applied to a product is just a layer of paint or plated metal and the finishing techniques for products actually vary. The most common finishing technique is chemical film coatings. This method has a lot of benefits when compared and then combined with other finishing techniques, and it is used in different industrial applications.
WHAT IS “CHEM FILM” OR CHEMICAL FILM COATINGS?
Chemical films are a common and inexpensive finish, that has been used by several different industries for different products as well as purposes. The chemical is a sealant, which adheres and alters the exterior of metal, which creates a thin film of material that protects the metal parts from corrosion. In most cases, the chemical film coating is the last step in the production process, but it is quite common to find chemical film coatings used to prime the surface for paint application.
Chemical film coatings, are also called chemical conversion coating, will result in different colors and finishes, which range from clear to iridescent colors to black, gold, green and blue. The darker that the color is, the stronger that the chemical film coating will be and the more resistance it will have to prevent corrosive forces, although there are some exceptions.
In addition to color, chemical films will vary based on their purpose and composition. In order to categorize chemical films, many companies will refer to the MIL-DTL-5541F specification from the military. This specification will organize chemical films into the following categories.
- TYPE 1 – This coating contains hexavalent chromium, which is why this process was originally called chromate conversion. While this was a standard recipe before the 21st century, exposure to this chemical is tightly regulated by OSHA and the EPA as a carcinogenic chemical in the United States.
- TYPE 2 – This type of coating doesn’t contain hexavalent chromium and is now becoming the standard in many industries. Normally hexavalent chromium is replaced with another chemical such as titanium, trivalent chromium, or zirconium.
- CLASS 1A – This class means that the purpose of the coating is to protect against corrosion, so the coat will tend to be darker and thicker to give improved protection. This class can also mean that the coating was used as a primer. These paints may be utilitarian or decorative. For instance, the military uses chemical agent resistant coating paint called CARC on vehicles and equipment as an added protection against chemical agents.
- CLASS 3 – This chemical film coating was designed to protect against corrosion and minimize interference with electrical conductivity. Normally, these coatings often have a lighter coating weight due to how thin it is when compared to the Class 1A coating.
The composition or type of film will determine just how effective the film can be on the material. It also will indicate any safety considerations that needed to be accounted for during the processing. The purpose of the film will help to determine the process that the film needs to be applied.
HOW DOES CHEMICAL FILM COATING WORK?
Chemical films will vary widely when it comes to composition and type, so the processes will vary based on the chemical film. However, the conversion coating process will follow a certain pattern:
- EDGE-BREAKING, CLEANING, AND POLISHING – Normal cleaning before chemical film coatings will involve a process that agitates and washes the part. First the part goes through a tumble bowl finishing process to edge-break and polish the part after it is made. The part will then go through an additional wash. Agitation in a powerful cleaning solution, followed by rinsing and drying is a way to clean the dirty parts. These processes make sure that dirt, oil and particulates that were formed during the packing or manufacturing process is removed before it is coated. This helps to guarantee maximum coverage and effectiveness of the chemical coating.
- ETCHING – If there are areas that the film shouldn’t be applied, then etching will handle it. After etching, the part will be rinsed again and a deoxy step is done to remove excess materials, chemicals, and contaminants.
- COATING – The chemical film is then applied after the part goes through the above processes. The amount of time that it will take for the coating to be applied will depend on the way that it is applied as well as the composition of the film. The material that the part is made from and the part size will also play a factor. Normally, Class 1A coatings will take longer to apply than a Class 3 coating, because of the increased thickness. The Chemical film process will normally use a barrel or rack coating process, which involves either immersion, brush, or spray coating technique.
The time that is needed to go through each of these steps will vary based on the part and the chemical film that is being used, but each part will normally take 10 minutes to 30 minutes to process.
WHAT MATERIALS WORK WITH CHEMICAL FILM COATING?
Chemical coatings will work with a variety of metals and materials. While the chemical composition of the film will vary according to the substrate, chemical films will offer various benefits to most materials. Some examples of the materials that benefit from chemical film coatings including:
- ALUMINUM – Although aluminum has a better than average existing protection from corrosion, such protection can be stressed with a suitable substance covering. Another, more unmistakable motivation behind chemical films on aluminum, in any case, is to enhance attachment of paints and prep coatings to the surface of an aluminum part. The two advantages of chemical film coatings are of incredible significance with regards to military and protection applications, as aluminum is an imperative material for the safeguard business. Truth be told, the MIL-DTL-5541F talked about above was composed principally for aluminum coatings.
- MAGNESIUM – Magnesium and its related amalgams are ending up progressively mainstream materials in aviation and car applications. Magnesium is to a great degree lightweight and highlights a noteworthy quality to-weight proportion, making it a to a great degree attractive material for an assortment of uses. The thickness of the material is telling — magnesium brandishes a thickness that is 66% that of aluminum and one-fourth that of iron. While profoundly attractive, magnesium sports an appalling proclivity for chemicals, responding contrarily with barometrical oxygen and water to make a permeable oxide carbonate film on the surface of the material. This consumes the metal, making it almost pointless in damp air. Magnesium compounds don’t passage much better in comparative conditions. To ensure against this consumption, a synthetic film can be connected to a magnesium part, enabling it to be utilized as a part of industry more viably.
- BERYLLIUM – This is a lightweight metal that is found in the earth’s crust and has a lot of useful properties such as a high melting point, natural resistance to corrosion and good thermal conductivity. However, beryllium also happens to be toxic, which can cause damage to the respiratory systems and human lungs. It is a useful metal, and it use in computer components, heat sinks, x-ray detection equipment, and satellite structures. In order to make the metal more acceptable for use, chemical films are often applied to the metal, which improves corrosion resistance and contains the material as much as possible.
- ZINC – This is the 4th most widely consumed metal in the world. Zinc is really useful and very corrosion resistant. It corrodes up to 100 times slower than other metals and it manages to avoid damage by producing zinc patina when it oxidizes. While this makes zinc perfect for plating, it does create an issue when the zinc is an important functioning part of the final product. To help to maintain the resistance of corrosion without having to sacrifice the surface of the coating or zinc, chemical films are applied to the surface which makes it less susceptible to oxidation.
Although, this is hardly a full list of materials that a chemical film coating may be applied to, these are just the most common materials that have chemical film coatings.
WHAT ARE THE BENEFITS OF CHEMICAL FILM COATINGS?
Chemical film coatings are often used with other types of finishing techniques, although, it is often just used by itself. The frequent usage has a lot to do with the benefits that the process has to offer, including:
- PROTECTION AGAINST EROSION – Industries ordinarily utilize concoction film covering as a defensive covering for parts made of an assortment of materials. From the metals recorded above to permeable plastics and glass, a concoction film covering anticipates consumption by adjusting the surface nature of about any material without adding to the volume of the part.
- LOW ELECTRICAL IMPEDANCE – Chemical movies don’t influence the electrical conductivity of a material. This is particularly valid for Class 3 concoction films. At the point when the motivation behind a section incorporates directing power, it’s critical that a covering not modify that reason. Not at all like some other covering or plating forms, synthetic movies make little difference to the conductive properties of the final result.
- RELATIVELY ECONOMICAL – Chemical film creates minimal waste and is moderately cheap to deliver contrasted with different strategies, making it a to a great degree alluring choice for cost-disapproved of organizations. Rather than a plating or covering with a large group of pointless qualities and highlights, organizations concerned just about erosion protection can discover a financially savvy choice in synthetic film coatings. This is particularly critical for organizations requiring high volumes of item.
- EASY APPLICATION PROCESS – The way toward applying substance movies and coatings is moderately straightforward, including almost no time and push to deliver an astounding covering. Moreover, the procedure is unendingly reproducible, making it perfect for large scale manufacturing.
Excellent cement properties: From plastics to metals, compound movies give a steady, thin coat to which cements and paints can immovably connect. Therefore, substance films are generally utilized as defensive preliminaries for an assortment of mechanical items that must later interpretation of a layer of paint.
WHAT INDUSTRIES BENEFIT CHEMICAL FILM COATINGS?
The benefits of chemical film coatings are not just lost on industrial products. A variety of industries use chemical film coatings for several things including:
- ELECTRICAL INDUSTRY – Electronic manufacturers use chemical films on housings for products, as protection against corrosion. This helps to ensure long term safety and stability of the internal and wiring components in the product.
- AEROSPACE INDUSTRY – Aerospace aviation will use chemical film coatings to repair any anodized surfaces. This is used to protect aircraft parts and components from corrosion. At high speeds, high up, a cloud can be corrosive to an airplane, which is why maximum protection is needed for as many parts as possible.
- MILITARY AND DEFENSE – Chemical films are used by the department of defense in many ways. From priming parts to protecting equipment. They use this finishing method as a standard which includes the MIL-DTL-5541F specifications for regulating and categorizing chemical film coatings and applications.
- MARITIME INDUSTRY – Boats and other watercrafts need to be corrosion resistant to protect their parts from water damage. This is vital for boats used in salt water environments. The anticorrosive properties of chemical films are highly sought after for this, in addition to the usefulness as a paint primer for custom painted watercrafts.
Many other specifications do exist, which specify and categorize requirements that are associated with various metals and their finishes.
WHAT FACTORS INFLUENCE CHEMICAL FILM COATING RESULTS?
The result of chemical film coating process will depend on various factors. These factors include:
- MATERIAL TYPE – The material type that the coating is applied to will also have an impact on the appearance of the product. A purer material will have different appearance from an alloy that is coated with the same chemical.
- MATERIAL QUALITY AND PURITY – The chemical nature of the chemical film coating means that any change to the recipe will result in a different outcome. For instance, purer aluminum alloys will provide a better resistance from corrosion after applying chemical film coating than a less pure alloy.
- SURFACE QUALITY – Whether the substrate surface is etched or polished will affect the uniformity of the surface when the chemical film is applied.
- CHEMICAL FILM CLASS – The class that the chemical film uses will have an effect on the end result. Class 1A chemical films will be thicker and darker, while Class 3 films are lighter and thinner.
The final appearance of the product is important, so talk with your coating provider to discuss options and even look at samples, or have a sample batch coated to find your preferences.
WHERE CAN YOU FIND CHEMICAL FILM COATING SERVICES?
We are one of the most trusted plating companies around. All of our plating services have taken years to hone and perfect when it comes to chemical film processes, which apply our years of experience in the industry to develop the best type of methods in application from rack plating to barrel plating. We work hard to help all customers by reducing costs and lead times as well as offering them the best product quality that is on the market. We aren’t just another plating company- we are a plating partner. To learn more about how you can benefit from professional chemical film coating services, contact us today for a free, no obligation quote.